Woven wire mesh is used in a huge number of applications in very diverse industries.
Thought can be to filtration, lamination, sieving, architecture or as reinforcement.
Depending on the use, we supply the specifications conform your requirements.
Parameters for woven wire mesh are alloy, wire diameter, mesh opening and weaving-execution.
Available in, for example, galvanized steel, stainless steel alloys, like AISI 304, AISI 316, AISI 321, AISI 430, brass or copper.
Furthermore we have materials like Inconel™, Incoloy™, Monel™ and Hastelloy™. in our delivery program.
Because of the weaving pattern, each mesh got its own characteristics. With weaving mesh openings of only 5 micron up to a few centimeters are possible.
Weaving methods
Mesh Masters supplies mesh for every required purpose.
The undermentioned image explains which parameters must be used.
- Mesh number is the number of meshes per specific length unit. Usually this number is stated per inch.
- Mesh opening (w) is the space between the adjecent two wires.
- Wire diameter (d) is the diameter of the wire before weaving
- Pitch (p) is the distance between the centero f the two adjecent wires.
- Warp wire is the tensioned wire that runs parallel to the self-side
- Weft wire is the wire that is braided perpendicularly through the warp wire
Depending of the application, the way of weaving is determinative for the selection of mesh.
A weave can get different properties by the way the warp and weft are connected.
In the overview below, the most used weaving patterns can be found.
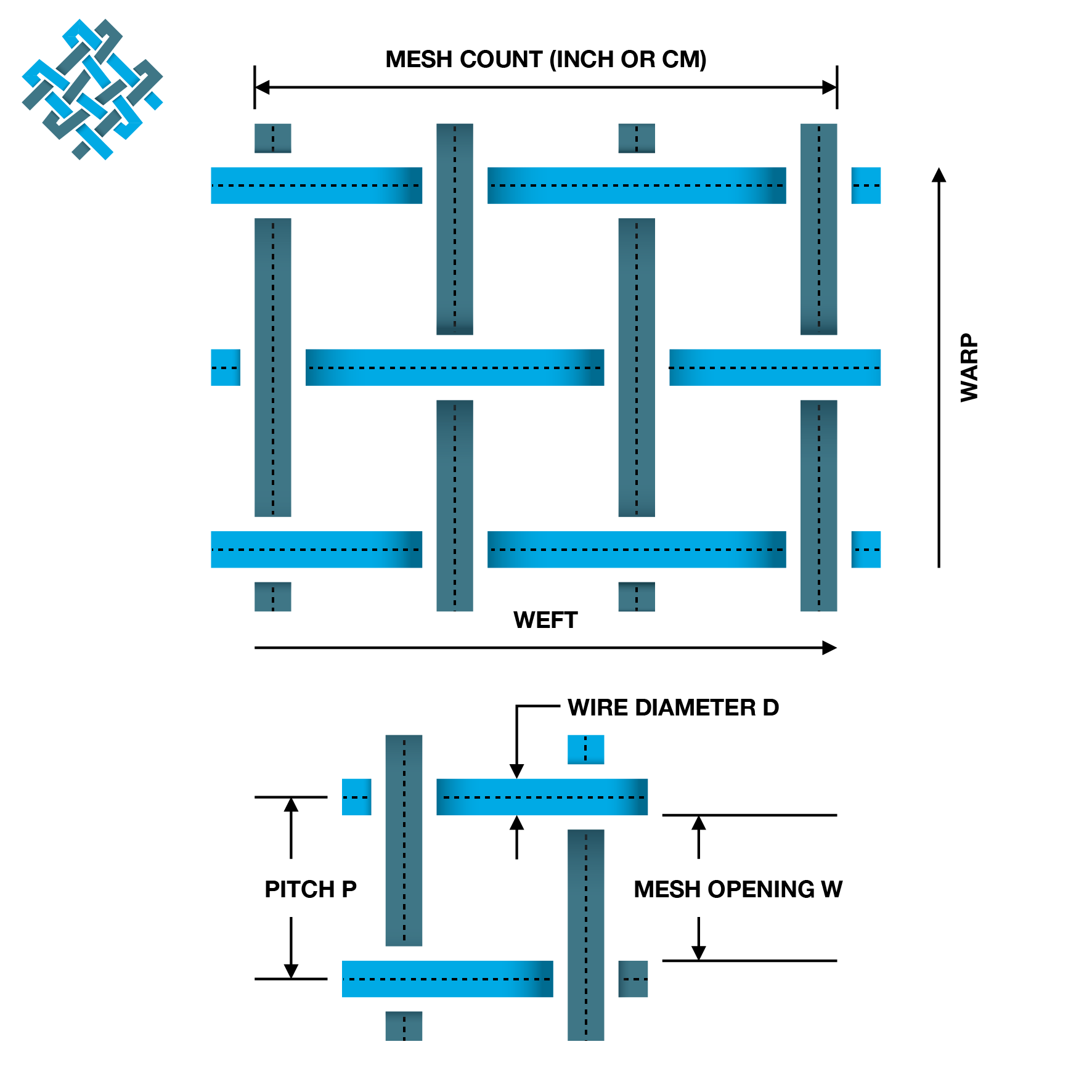
Plain weave
The most used and common way of weaving.
In this way of weaving, the wires lie alternately over each other.
The wire diameters of the warp and weft are the same here.
The smallest mesh opening we can supply with plain weave is 25μm.
Twilled weave
Weaving in this way, the wires are first woven over and then over two wires.
This creates a diagonal weaving pattern that is characteristic of this weave.
Twill weave offers the possibility to use a thicker wire without distorting it during weaving.
This makes the mesh more stable.
The smallest opening for a twill weave mesh is 20μm.
Dutch plain weave
A weaving technique in which the weft wire of the fabric has a smaller diameter than the warp wire.
The warp wire can therefore lie closer to each other so that virtually no mesh opening is created.
As a result, the mechanical strength of the mesh is many time higher than, for example, a plain weave.
Dutch plain weave is often used in industrial filtering where a high rigidity of the mesh is required.
The minimum opening we can supply for a Dutch Plain Weave is 45μm.
Dutch twilled weave
A combination of twilled weave and Dutch plain weave is used for this type of weaving.
With this weaving technique, the weft wire has a smaller diameter than the warp wire and the warp wires are closer to each other.
Here, just like twilled weave, the wire are not woven alternately, but in pairs.
This makes the mesh very strong in proportion to the fineness.
Because of these properties, this mesh is mainly used for heavy filtration.
The minimum opening for a Dutch Twilled weave we can offer, is 5μm.
Crimped woven wire mesh
In the overview below, a selection of our meshes can be found which are produced conform the ISO 4783-3 standard.
This mesh is woven with a pre-crimped, and generally, a thicker wire.
Depending on the execution, this mesh has got a better wear resistance, better resistant to vibrations and is the mesh opening dimensionally stable.
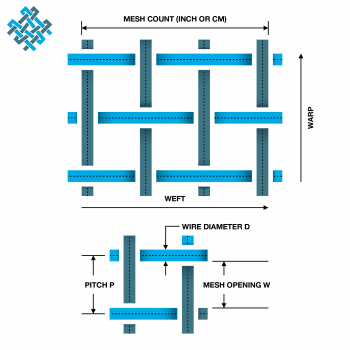
Type I
Standard execution for crimped woven wire mesh.
Suitable for vibrating screens for example.
Type II
This type is executed with a pleat in the wire.
It is common to use this wire with large mesh sizes..
Type III
In this embodiment, the mesh is pressed flat on one side.
This makes the mesh better resistant to wear on sieving machines.
Type IV
With this execution, the mesh is pressed flat on both sides.
This treatment ensures that the mesh opening of the mesh retains in its shape.